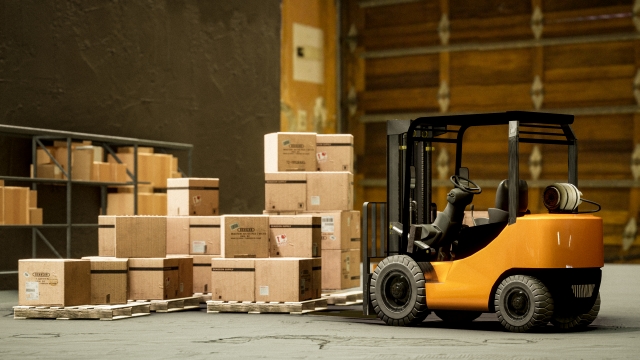
EC事業における出荷業務では、配送ニーズの多様化やECの需要拡大などによる作業負担の増加が深刻化しています。出荷業務が滞ると、配送遅延や出荷ミスを引き起こし、顧客の信用を失う事態にも発展しかねません。
そこで本記事では、出荷業務効率化の必要性やメリットをご紹介します。出荷業務を効率化させるための対策方法についても解説するので、ぜひ参考にしてください。
なお、出荷管理の基礎知識については、以下の記事で詳しく解説しているので、あわせてご覧ください。
出荷業務で発生しやすい3つのトラブル
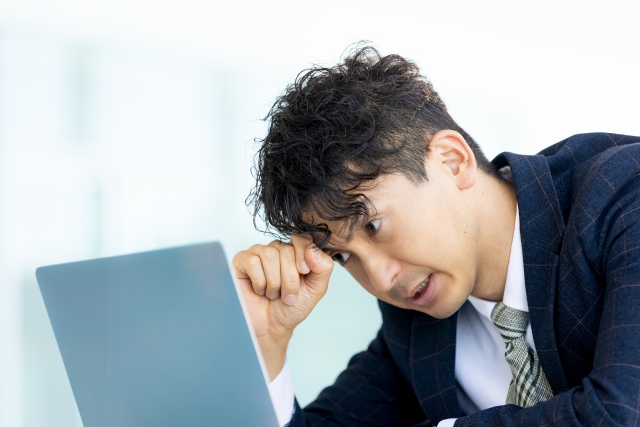
日々膨大な作業量をこなす出荷業務では、さまざまなトラブルが発生します。トラブルはそのまま出荷ミスへとつながり、顧客からクレームを受ける事態に発展するので、まずはどういったトラブルが発生しやすいのか把握しておくことが大切です。
以下に、発生しやすいトラブルを3つ解説するので、ぜひ参考にしてください。
注文情報の管理ミス
注文情報の管理ミスとは、顧客の注文内容に沿わない形で出荷を進めたり、注文情報を出荷のステータスに進めずに放置していたりする際に発生するミスです。具体的には、以下のようなミスがあります。
- 注文情報が受注ステータスのままになっている
- 商品の種類や数量の転記ミス
- 備考欄の確認漏れ
注文情報のステータスの更新漏れは、受注管理システムを使用している際に発生するミスです。出荷ステータスに移行せず、注文をそのまま放置しているので、商品の発送が遅れてしまいます。
また、転記ミスや備考欄の確認漏れは、手動で注文処理を行っている際に発生するミスです。手動の注文処理は効率が悪く、ミスも発生しやすいので、業務フローやシステムを見直す必要があります。(ご参考:「備考欄チェック作業を効率化しよう!【働くネクストエンジン – 受注処理篇】」)
ピッキングのミス
ピッキングとは、注文された商品を倉庫内から集めてくる作業のことです。在庫量や受注件数が多いと、ピッキングミスは高頻度で発生します。
とくに多いのが、商品のカラー違いやサイズ違い品をピックしてしまうケースです。ピッキングリストを見ながら、目視で確認していると、商品の取り違えや確認ミスがどうしても発生します。
検品・梱包・出荷時のミス
商品を出荷する際は、ピッキングした後に検品を行い、梱包してから出荷するのが基本フローです。検品は出荷業務の最後の砦になるため、検品や梱包のミスはそのまま出荷ミスを引き起こします。
出荷時のミス事例を以下にまとめました。
- 商品の梱包漏れ・商品の過剰出荷
- 宛先ラベルの貼り違え
- 伝票・納品書の取り違え
検品や梱包は1件ずつ処理していくのが基本ですが、検品台の上に複数の注文分をまとめて置いてしまい、商品が混ざってしまうことがあります。また、前の注文分で納品書を入れるのを忘れ、次の注文分に誤って封入してしまうケースもあるので注意しましょう。
非効率な出荷業務がもたらすリスクとは
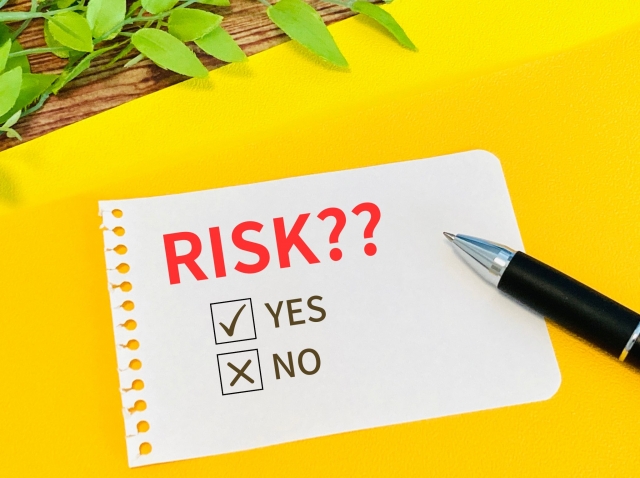
出荷業務の効率が悪いと、作業現場に時間的・体力的に多くの負担をかけることになります。その結果、さまざまなミスを引き起こし、企業にとって多くのリスクをかかえることになるので注意が必要です。
以下で、非効率な出荷業務がもたらす4つのリスクを紹介するので、ぜひ参考にしてください。
在庫の過多・不足
非効率な出荷業務を行っていると、出荷ミスが多くなり、在庫の過不足が発生します。在庫が不足していると、欠品による販売機会損失を引き起こす可能性があるので、売り上げの低下を招きます。
一方、過剰在庫が発生したケースでは、原因の確認に手間取るほか、保管スペースを圧迫しかねません。定期的に行う棚卸しで確認の手間が増えるなど、在庫の過不足が原因で、さらに業務効率が悪化します。
過剰在庫については以下の記事でも解説していますので、ぜひ参考にしてください。
顧客の個人情報の漏洩
出荷業務の非効率さが原因で、宛名や伝票間違いなどのミスを引き起こすと、顧客の個人情報が漏洩してしまう可能性があります。
悪意を持った第三者に個人情報を不正に利用されてしまうと、個人情報保護法に抵触した企業として公表され、信用を失う事態にもなりかねません。
クレーム処理にかかる時間やコスト
出荷ミスが発生した後は、正しい商品の再発送や商品の引き取り業務など、それぞれ適切なフォローが必要です。
また、電話によるクレーム対応やお詫びのメール作成を行う手間も増えます。ミスがなければ行う必要のない余計な業務が発生するので、追加のコストがかかります。
企業イメージの悪化
配送遅延や出荷ミスが度々発生すると、顧客の信用を失います。たとえ実用性の高い商品を販売していたとしても、あえてトラブルの多い企業から商品を購入したいと思う人はほとんどいません。
とくに、ECサイトでは「違う商品が入っていた」「指定日に間に合わなかった」などの悪いレビューが、企業イメージを大きく悪化させるケースも珍しくありません。
出荷業務効率化がもたらすメリット
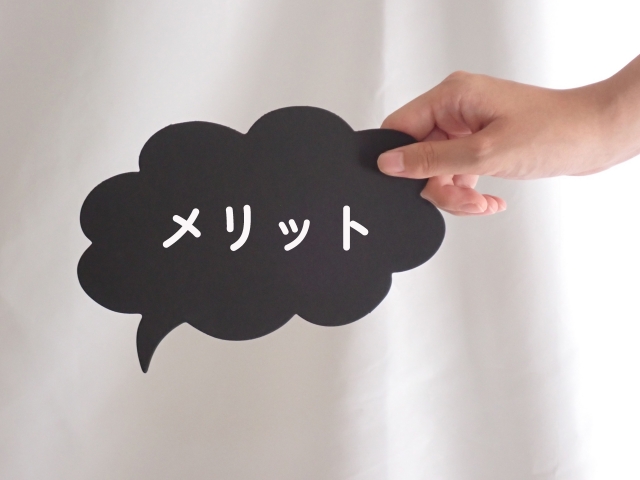
出荷業務の効率化が進むと、作業現場の業務負担が減るだけでなく、付随して多くのメリットをもたらします。
ここでは、3つのメリットを紹介するので、ぜひ参考にしてください。
ほかの業務にリソースを割けるようになる
出荷業務が効率化されると、出荷ミスなどによる余計な業務が発生しなくなります。その結果、余ったリソースをほかの業務に割くことが可能です。
自社で商品を企画・開発しているのであれば、よりよい商品を開発し、魅力的なイベントを企画できるようになります。
業務全体の効率改善につながる
出荷業務が効率化されると、余った人員や時間的リソースをほかの業務に回せるようになります。入庫業務の人員を手厚くすれば、入庫から棚入れまでのリードタイムを短くすることも可能です。
人件費を削減できるなど、業務全体に好循環が生まれるので、さらに売り上げや利益を確保できるようになるでしょう。
顧客満足度の向上が見込める
正確かつ迅速な出荷処理を続けていれば、顧客満足度の向上が見込めます。商品を継続購入してくれるリピーターの確保につながるので、売り上げや利益を拡大することが可能です。
ただし、顧客満足度は一朝一夕で向上するものではないので、日々の積み重ねを大切にしましょう。
出荷業務改善に取り組むときの手順
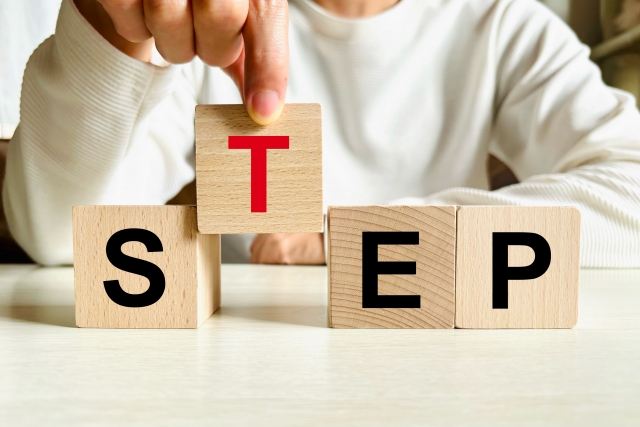
出荷業務改善に取り組む際は、順序を立てて、計画的に行うことが大切です。
ここでは、出荷業務改善手順を3ステップに分けて解説していきます。
1.現状把握と問題点の洗い出し
まずは、現状把握を行い、問題点を洗い出します。問題点が浮き彫りでなければ、効果的な改善案が浮かばないためです。
現状把握を行う際は、出荷業務を工程ごとに分類分けし、それぞれの作業にかけている時間や人員を把握しましょう。
出荷業務の工程は、以下の4つに分けられています。
- 受注処理
- ピッキング
- 検品・梱包
- 仕分け・積み込み
工程ごとの生産性を集計し、効率の悪い業務や問題点を洗い出しましょう。
2.改善施策の検討と実行
問題点を洗い出した後は、改善施策の検討を行います。
出荷現場でよくある問題点と解決方法を以下にまとめました。
問題点 | 解決方法 |
ピッキングに時間がかかる | 倉庫内レイアウトの見直し |
人員が足りていない | ・人員の増員 ・マテハンやシステムによる業務の自動化 ・アウトソーシングの活用(外注) |
作業者によって処理件数に大きな差がある | 業務フローの確立や作業マニュアルの作成 |
1度に複数の改善策を実行すると、現場の戸惑いも大きくなるため、優先順位をつけてひとつずつこなすことが大切です。現場の作業員と相談しながら、改善施策を実行しましょう。
3.効果の検証と有用な施策の仕組み化
最後に、業務改善後の効果を検証します。工程ごとの生産性を集計し、改善前の生産性と比較してみましょう。
おもな評価基準は、以下の通りです。
- 1時間あたりの処理件数が増えたか
- 以前よりも少ない人員で業務をこなせるようになったか
- 費用対効果は高いか
なお、効果検証は数値だけでなく、現場の声を拾うことも大切です。作業効率がよくても、作業者の負担が増えていれば、あまり意味がありません。
有用な施策は仕組み化し、引き続き業務に取り入れましょう。
出荷業務の効率化に効果がある8つの対策
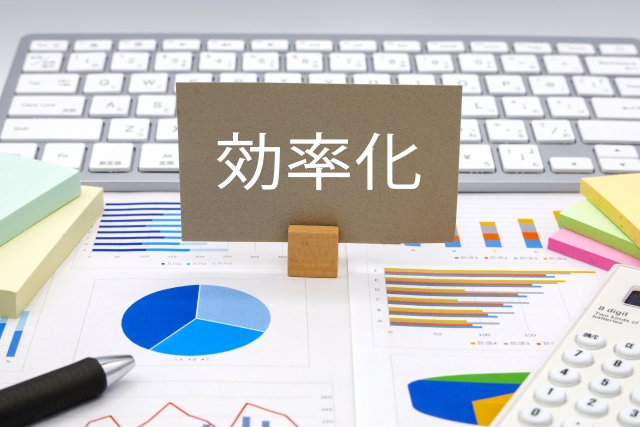
出荷業務を効率化させる方法は、多岐に渡ります。
8つの対策方法を紹介するので、自社に適した方法を取り入れてみてください。
(1)出荷業務フローのマニュアル化
マニュアル化されていない業務は、作業者単位で手順が異なるため、品質や効率に大きな差が生じます。よって、出荷業務フローをマニュアル化し、作業手順を全作業者で統一することが大切です。
作成したマニュアルは、目立つ場所に掲示し、初めて出荷業務を行う方でも問題なく作業できる体制を整えましょう。
(2)ピッキング方法の見直し
出荷業務のなかで最も作業負担が大きく、改善の余地があるのはピッキング作業です。ピッキング作業を見直すことで、後の工程でもミスが出にくくなり、出荷業務全体の効率化が進みます。
なお、ピッキングには、オーダーピッキング(摘み取り式)とトータルピッキング(種まき式)の2つの方法があるので、自社の業務に適した方法を選択することが重要です。
オーダーピッキングは、注文1件単位で商品を集めて梱包する方法で、宛先の多いECでは基本的にオーダーピッキングが適しています。
また、ピッキングはピッキングリストを発行して、目視で商品を確認するのが従来の方法ですが、ハンディターミナルやスマートフォンを活用すれば確認作業の効率や品質が向上します。
商品バーコードやロケーションコードを読み込み、注文情報と照らしあわせれば、目視で確認する手間やピックミスの可能性を軽減することが可能です。
ピッキングについては以下の記事でも詳しく解説していますので、ぜひ参考にしてください。
(3)倉庫内の整頓
倉庫内が散らかっている状態では、作業員の足取りが重くなり、ピッキング作業を中心に作業効率が悪化します。おもに入庫量が増加し、ロケーションに在庫が収まらないケースでよくある光景です。
このような事態に陥らないためにも、日頃からロケーション整理を行い、在庫の空きスペースを確保しておきましょう。
5Sを徹底して作業場を整頓しておくことも重要です。5Sとは、整理・整頓・清掃・清潔・しつけの頭文字を取った用語で、物流業界でよく使用されます。
(4)作業動線の短縮
作業導線が長ければ、ピッキング時の移動距離が長くなるので、出荷作業の効率が悪くなります。したがって、作業導線を短縮し、作業者がなるべく歩かない体制を整えることが重要です。
例えば、一緒に購入されやすい商品のロケーションをまとめる方法が有効です。セットアップ商品はもちろん、同品番のアイテムはなるべく近くに配置するとよいでしょう。
また、ピッキングリストによってピックする順番を指定し、作業者が一定方向にのみ歩いてピックできる体制を整えるのもおすすめです。
(5)人員配置の適正化
作業者一人ひとりによって、得意・不得意があるため、人員配置によって作業効率は大きく変化します。したがって、それぞれの特性を見極め、各工程に配置する人員を適正化することが大切です。
人員配置を適正化するためには、出荷現場の管理者育成が鍵を握ります。管理者の業務や作業者への理解度が高ければ、人員配置を適正化することが可能です。
(6)マテリアルハンドリング機器の導入
マテリアルハンドリング機器(通称マテハン)とは、荷役機器を中心に、物流業務を効率化するために用いられる機器全般のことです。ベルトコンベアや自動搬送システムはもちろん、台車やカゴといった小規模なものも該当します。
マテリアルハンドリング機器を導入すれば、人の手によって行う作業量が減少するので、出荷業務効率の大幅な向上が期待できます。
(7)在庫管理の適切化
在庫管理を適切に行えば、商品を探す手間やピッキングミスが減るので、出荷業務が大幅に効率化されます。また、作業導線の確保にもつながるので、よりピッキング効率を高めることが可能です。
在庫管理は、出荷業務に限らず、すべての業務の起点となるので、日頃から在庫管理を徹底しましょう。
(8)在庫管理システムの導入
在庫管理システムを導入すれば、在庫管理の効率化が進み、結果的に出荷業務の効率が上がります。
また、商品の保管場所を素早く確認できるようになるほか、ピッキングリストを自動発行して効率のよいピッキングを行うことも可能です。
ただし、在庫管理システムの導入には、一定のコストがかかるので、導入するシステムは慎重に検討しましょう。
在庫管理システムについては以下の記事でも解説していますので、ぜひ参考にしてください。
まとめ:リスク回避のためにも出荷業務の効率化を図ろう
EC事業における出荷業務は、顧客満足度や企業の信用を左右する重要な業務です。配送遅延や誤出荷などが頻繁に発生すると、企業イメージを悪化させてしまいます。
このようなリスクを回避するためにも、本記事で紹介した8つの対策方法から適切な施策を選び、出荷業務の効率化を図りましょう。
以下に「物流のいまとこれから」をまとめた資料を無料で公開しています。お気軽にご活用ください。
出荷業務をラクに!受注処理~出荷までネクストエンジンにお任せください
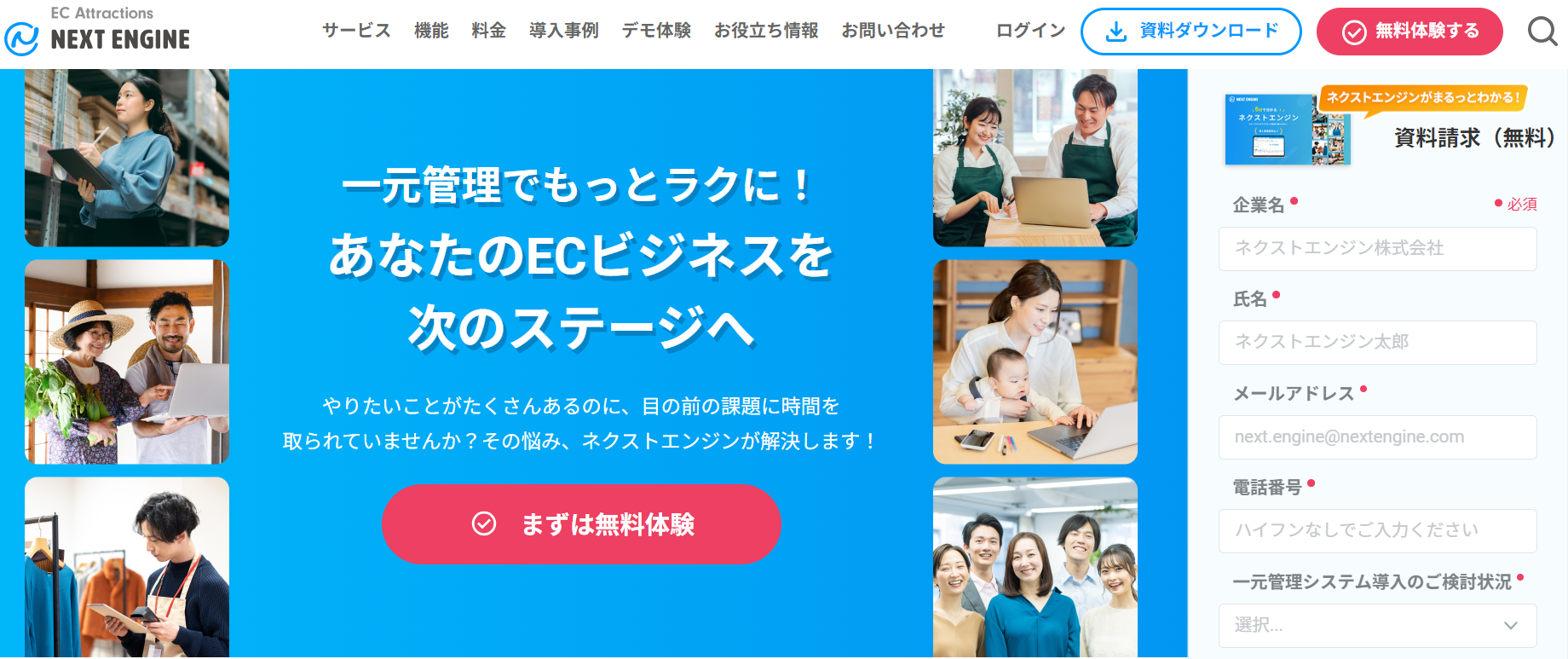
「ネクストエンジン」は、EC運営を効率化するために開発された、EC一元管理システムです。受注管理や在庫管理をはじめ、EC運営にまつわるさまざまな業務をラクにする豊富な機能を備えています。
ネクストエンジンのおもな機能は以下の通りです。
など
出荷業務は、煩雑なコピペ作業や納品書の発行作業など、細かなルーチンワークが数多く存在します。ネクストエンジンなら、これらの業務を自動化・効率化できるので、出荷業務全体の効率化が可能です。
例えば本記事内で出荷ミスの原因の1つとして挙げられていた「備考欄確認のミス」について、ネクストエンジンなら、伝票を一つずつ確認する手間をできるだけ省けるよう「備考欄変換設定」機能を搭載しています。
詳しくは以下の記事をご参考ください。
また、ネクストエンジンはダッシュボードに「自動出荷率」を表示する取り組みを開始しています。自社の当月の自動出荷率や前月との比較を確認できるほか、ネクストエンジンを利用する企業の平均自動出荷率も確認できます。
ネクストエンジンの出荷管理について詳しく知りたい方のために以下に資料をご用意しておりますので、お気軽にダウンロードしてください。